3D Printing: COVID-19 Face Shields
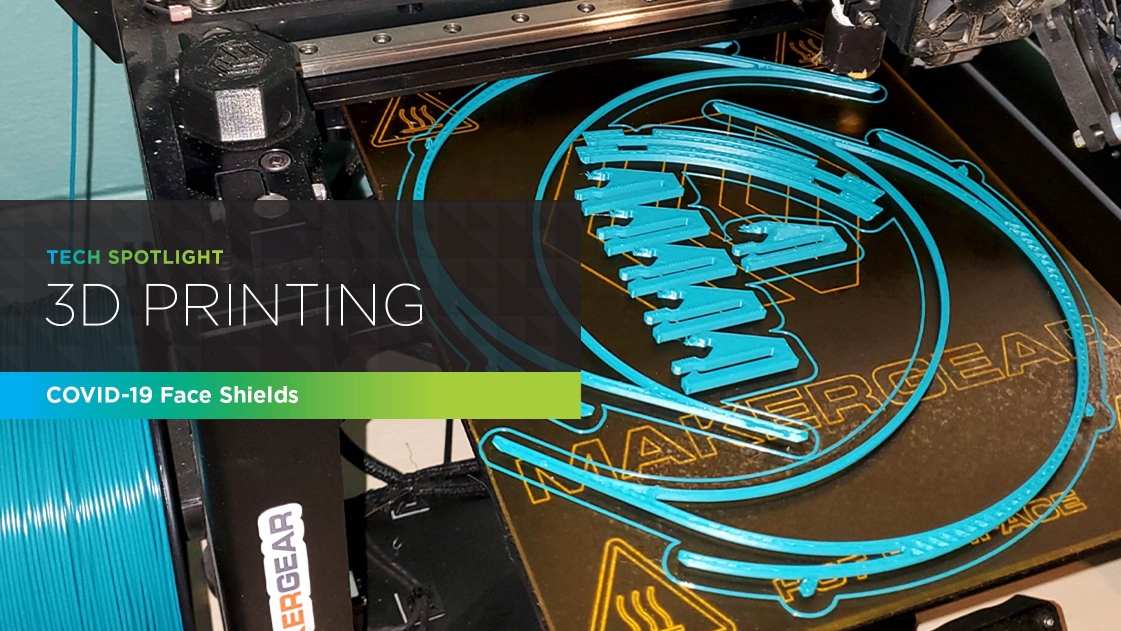
In our recent GIS Tech Spotlight blog, we highlighted some of the amazing technology tools available in our industry, and how we’re using them at OHM Advisors through a variety of applications to help solve our clients’ challenges. A key point we touched on was the truly unlimited potential of technology—how we’re using these tools in innovative ways to help create impactful solutions for the people we serve.
In the wake of COVID-19, we were thrilled to use our 3D printing technology to help a combined effort by the office of Oakland County Water Resources Commissioner to print PPE face shields for front-line healthcare workers. As of the date of this publication, the combined effort has provided over 1200 face shields to medical providers across Michigan, Florida, New Mexico and throughout New York City. It’s our small contribution to the world’s response to a big problem, but we hope it helps.
Here’s how we did it.
3D Printing Technology: What is it?
As its name suggests, 3D printing is a manufacturing process that can build three-dimensional objects out of a variety of materials to be used in the real world. They’ve been used for years in design studios and on workshop floors, in schools and community centers and by hobbyists, but have become commercially available for a range of personal and business uses today.
The technology manufactures 3D objects through a layering process in which the material used—whether plastic, metal or other material that can be reduced to liquid form—is created layer by layer to form the final product. The process begins with a digital file containing three-dimensional data, created on a computer-aided design (CAD) or computer-aided manufacturing (CAM) program or 3D scanner, which is then converted into a print model through 3D printing software and then produced by the printer as a physical object.
For the tech savvy, we currently use a MakerGear brand, M2 Rev F model with a dual head extrusion and 8”L x 10”W x 8”H build platform at OHM Advisors.
PPE Face Shield Printing
Manufacturing one PPE face shield requires the 3D printing of multiple components that are combined to create the final product. To create this particular face shield, a CAD model first needs to be made for each component of the shield.
After the pieces have been 3D modeled by CAD, the file is exported to be sliced by software—appropriately called “Slicer”—in which the modeled pieces are assigned layers by millimeters and a 3D print path is generated.
Once the digital preparation is complete, the process of 3D printing can begin. First, a roll of filament material—plastic, metal or other—is loaded into the heated extruder. The extruder pulls in the filament and forces it through a heated tip, moving along the designated path from the Slicer software while continuously expressing liquified filament. The liquified material cools and solidifies in place at varying times based on the on the type of filaments used.
From this point on, the printer operator observes the print process for flaws that will cause the print to fail. If a print fails early on in the process without being noticed, the printer operator will return to find a solidified “form” that is definitely not what the CAD model intended! Barring any failures, the pieces are assembled to create the final PPE face shield.
We’re excited to have participated in this combined effort to get our front-line healthcare workers the equipment they need to do their essential medical work during this pandemic.
To learn more about how we’re using technology like 3D printing in unique ways, watch for future Tech Spotlight posts, sign up for our e-newsletter, or contact one of our specialists today at advancingcommunities@ohm-advisors.com.